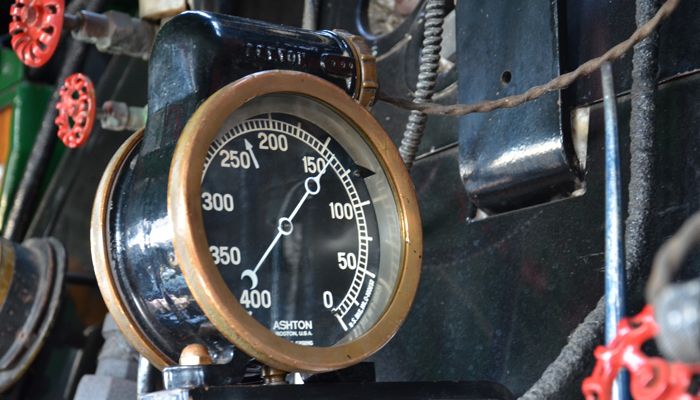
The 3751 was a pioneer 4-8-4 locomotive for both the Santa Fe Railroad and the Baldwin Locomotive Works. As such, extensive testing was done on the locomotive during its first years on the railroad. The first set of mechanical articles presented below were taken from the June 2, 1928 issue of “Railway Age” and written about the 3751-class prototype locomotive (#3751) after its first year of active operation on the Santa Fe Railroad. The second set of articles are from the September 1939 issue of “Railway Mechanical Engineer” and focused on the overhauls performed on the 3751-class locomotives.
“Railway Age” Articles
Santa Fe 4-8-4 Type Meets Expectations
With the principal object of handling heavier passenger trains faster and with less unit fuel consumption, the Atchison, Topeka & Santa Fe designed and placed in service during the past year, 10 modified Mountain type coal-burning locomotives of 4-8-4 wheel arrangement, known on the Santa Fe as the 3751 class, and numbered from 3751 to 3760 inclusive. These locomotives, built by the Baldwin Locomotive Works, are of the two-cylinder single-expansion type, equipped with 30 in. by 30 in. cylinders and 73 inch driving wheels, and develop 66,000 lb. tractive force at a boiler pressure of 210 lb. without the aid of a booster.
The new locomotive is notable for high boiler capacity, evaporating in one test an average of 6.74 lb. of water per lb. of coal when burning low-grade Colorado mine run at the rate of 4,125 lb. of coal an hour. The combustion chamber firebox, with a total grate area of 108 sq. ft. and round-hole table grates, is designed to assure a low rate of firing per sq. ft. of grate area and as nearly complete combustion as practicable before the gases pass into the flues. In order to accommodate this large firebox, a non-articulated four-wheel trailing truck, which has been in the process of development on the Santa Fe since 1919, is applied. Driving axle loads up to 70,600 lb. are used on certain pairs of wheels, yet without excessive rail stress on either tangent track or curves, due to careful spring equalization, proper counterbalancing of the reciprocating and revolving weights and cross counterbalancing the revolving weights on the main wheels to offset the effect of these weights moving in different planes.
Favorable Operating Results Secured
Operating results secured with the 3751-class locomotive under actual service conditions have exceeded the expectations. This locomotive has demonstrated the ability to start 26 cars of heavy modern equipment on level track, or 15 cars on a 1.13 per-cent grade, in the latter case accelerating to a speed of 20 to 25 miles per hour in a distance of 15 car lengths. In the mountain country of Colorado, New Mexico and Arizona, the locomotive handles 15 cars over grades up to two per cent and 9 cars over the 3 1/2 per-cent grade of the Raton Mountains, without a helper. Sixteen-degree curves can be negotiated. The locomotive is said to handle easily, accelerate rapidly and ride easily, especially on curves, which the locomotive is designed to pass with a minimum of flange and rail stress and nosing.
In general, because of slack business, the new locomotives have not been operated to full capacity since being placed in service and, consequently, maximum results with respect to fuel economy could not be expected. A good indication of their performance is afforded, however, by the results of comparative tests of locomotive No. 3751 and locomotive No. 3714, a previous Santa Fe Mountain type locomotive, on the 347.5 mile run between La Junta, Colo., and Albuquerque, N.M. These tests were made during the latter part of 1927, operating in both directions between the two points mentioned.
It will be noted that locomotive No. 3751 handled four more cars at a slightly higher average speed than No. 3714. It handled, on average, 33 per cent more tons per train and developed a proportionately greater number of ton-miles. In making comparisons of fuel consumption, consideration must be given to the fact that locomotive No. 3714 is not equipped with a feedwater heater and accordingly, should be credited with about 10 per cent better performance. The balance of the improvement shown by locomotive No. 3751, however, is due to improvements in design, and amounts to a saving of roughly one-third of the fuel per unit of work which locomotive No. 3714 consumes under the most favorable circumstances. It will be noted that locomotive No. 3751 evaporated an average of 930 lb. of water and burned 138.6 lb. of coal per 1,000 ton-miles, or at the rate of 6.74 lb. of water per lb. of coal during these tests. All tests were made burning Colorado and New Mexico mine-run coal on round-hole table grates with 16-per-cent air openings.
Track Stress Limited
As a result of studies made on the Santa Fe during the past few years with a view to determining the wheel loading, distribution of weights and method of counterbalancing which will keep track stress within safe limits, a loading of trucks and driving axles of locomotive No. 3751 was adopted. For purposes of comparison, the wheel loads of locomotive No. 3710, a previous Santa Fe Mountain type locomotive, are also compared.
All of the driving wheels on locomotive No. 3751 have flanged tires, and no driving box lateral motion device is provided. The tires on No.1 and No. 4 wheels are set 1/8 in. nearer together than on the main and No. 3 wheels. Three-eighths inch lateral motion is provided on the front truck wheels, 3/16 in. on all drivers and on the forward trailer truck wheels, and 3/8 in. on the back wheels of the trailer truck. In general, the maximum static loads were kept to 70,000 lb. per axle and the combined static and dynamic loads to 76,000 lb. per axle. The effectiveness of this design, together with accurate cross counterbalancing and a division of the trailer-truck load between two axles, has been such as to permit increasing driving-axle loads almost 10,000 lb. in locomotive No. 3751 as compared with locomotive No. 3710 and at the same time to develop lower peak track stresses.
The comparative effects of these two locomotives on tangent track at 60 miles per hour are plainly shown in Chart I which gives the equivalent static load on each pair of drivers through a complete revolution. A glance at the chart shows that in locomotive No. 3751, the No. 1 driving wheels have been made to take more nearly a fair share of the equivalent static load than was the case with locomotive No. 3710, and as a result, the main and particularly the No. 3 wheels have been relieved of excessive loading. The chart shows that locomotive No. 3751 at 60 miles per hour on tangent track provides about 3,000 lb. less maximum equivalent static load on the rails than locomotive 3710, in spite of having from 9 to 15 per cent greater individual driving axle loads.
The stresses in both rails occasioned by locomotive 3751 passing a 10-deg. curve at three different speeds are examined. In general, the comparison indicates that the loads are fairly well distributed between the driving wheels and trucks under all curve and speed conditions; at least excessive peak loads from any one pair of wheels are avoided. Similar comparisons to those reproduced here for locomotive No. 3751 were developed for locomotive No. 3710 and published in the 1926 proceedings of the American Railway Association, Mechanical Division. In fact, the results of the tests reported at that time served as the basis for the distribution of the wheel loads in the present locomotive.
To illustrate how peak rail loads have been avoided by the design of locomotive N. 3751, a reference to the diagram for locomotive N. 3710, published in 1926, shows that at five miles an hour the No. 3 driving wheels cause a stress of about 46,000 lb. per sq. in. on the outside edge of the base of the inner rail on a 10-degree curve. With locomotive No. 3751, this stress at the slightly greater speed of 10 miles an hour has been reduced to 32,000 lb. per sq. in., as indicated in Chart II. At 25 miles an hour on the same curve, the No. 3 wheels of locomotive No. 3710 cause a maximum rail stress of about 35,000 lb. per sq. in., whereas the No. 3 wheels on locomotive N. 3751 cause a stress of only 32,000 lb. per sq. in. The records show that the trailer wheels of locomotive No. 3710, in passing a 10-deg. curve at 25 or more miles an hour, introduce a stress in excess of 40,000 lb. per sq. in. in the outside edge of the base of the outer rail. The trailer truck design on locomotive No. 3751, with the division of the load between two axles and a substantially shorter distance between the No. 4 driving and No. 1 trailer wheels, overcomes this difficulty.
General Description
In conjunction with the desire for high capacity, fuel economy, and reduced track stress, an effort has been made in the design of the Santa Fe 3751-class locomotives, to produce a type which requires less maintenance expense than some of its predecessors. Although no definite figures are available, this has undoubtedly been accomplished to a considerable degree, since locomotive design which reduces the destructive effect on track and roadway must necessarily involve the equalizing of unbalanced forces in the locomotive structure itself and consequently reduce wear and tear and resultant maintenance.
The 3751-class locomotive is equipped with one-piece cast steel cylinders and a separately cast Commonwealth bed frame. A Type E superheater with American multiple throttle is installed, also Nicholson thermic siphons in both the firebox and combustion chamber. The Elesco feedwater-heater installation includes a centrifugal pump designed to avoid pulsations which, under certain conditions, accentuate foaming difficulties. Other equipment on this locomotive includes the Ragonnet power reverse gear, Walschaert valve gear with multiplying lever to give nine inches maximum valve travel, Layden four-ported exhaust nozzle, 25 1/2 in. diameter smokestack and insulated smokebox.
An auxiliary dome, just ahead of the main steam dome and slightly to the left of the boiler center line, carries the safety valves and affords entrance to the boiler without removing the dry pipe. Dual sand boxes and equipment, including Graham-White sanders, give ample capacity and reliability for long distance mountain runs. Locomotives Nos. 3752 to 3756 inclusive, have Dupont stokers and Franklin butterfly fire doors. Locomotive Nos. 3751 and 3757 to 3760 inclusive, have Duplex stokers and Franklin vertical lift fire doors.
Alloy steels are used to a limited extent in the construction of these locomotives. The main driving wheel centers are of high tensile strength steel. The hollow main crank pins, as well as the piston rods, are made of oil-quenched and tempered chrome-nickel steel. Main and side rods and crank pins, other than the main, are carbon steel, normalized. Steam-pipe and superheater bolts in the smokebox are made of chrome-nickel steel, heat treated. Phosphor-bronze driving box brasses and nickel-bronze floating rod bushings are used.
The locomotive tender is constructed with a Commonwealth one-piece cast steel underframe having end sills cast integral and designed to accommodate the Franklin unit drawbar arrangement. Six-wheel trucks are applied, with cast steel side frames having riveted liners on the pedestal wear faces. Tatum-Zell type journal boxes are used. The tender has a capacity for 15,000 gal. of water and 20 tons of coal. The general dimensions of the new locomotive, as compared with a previous mountain type locomotive.
Cylinders and Running Gear
The cylinders of the 3751-class locomotive are combined in a one-piece steel casting representing a saving in weight of approximately 25 per cent over cylinders of cast iron. This steel cylinder casting is bolted and keyed to a locomotive bed and cradle frame cast of steel in one piece, with separate steel front deck casting in order to facilitate repairs in case of accidental collision. The steam and exhaust passages of the cylinders are designed free from restrictions and obstructions to the flow of steam. The exhaust passages are gradually reduced in area from the valve bushings to the base of the exhaust pipe in such a way that the cross section at no point is larger than a preceding section. All fillets have at least � in. radius.
The front engine truck is of the constant-resistance type with Commonwealth cast-steel frame, 33-in. solid rolled steel wheels, and 6-in. by 11-in. journals. The trailer truck is of the four-wheel Delta type with constant-resistance rockers and has a one-piece cast-steel frame. Both pairs of trailer wheels are 40 in. in diameter, the journals being 9 in by 14 in. Brass pedestal wearing liners are riveted to the truck frame.
The driving wheels are 73 in. in diameter, and in order to apply a boiler of the desired diameter and capacity, it was found necessary to use driving springs with reverse camber. The driving wheel centers are 66 in. in diameter and mounted on hollow-bored axles, the main axle being 13 in. in diameter and the others 12 in. The main crank pin is also hollow-bored with a four inch hole to reduce weight and provide for delivery of grease under pressure to the center of the main and side rod floating bushings. Flange tires are provided on all driving wheels, spaced as follows: Front wheels, 53 1/8 in.; main wheels, 53- in.; No. 3 wheels, 53- in.; No. 4 wheels, 53 1/8 in. Revolving weights and 50 per cent of the reciprocating weights are counterbalanced, revolving weights in the main wheels being cross-counterbalanced.
The static and dynamic load on these wheels is kept under 76,000 lb. per pair of wheels. The driving boxes have a bearing 13 in. long on the journals and are equipped with phosphor-bronze brasses with babbitt inserts and Elvin grease cellars. The shoes and wedges are also made of phosphor bronze. The normalized carbon-steel main rods have floating bushings on the back ends and front ends tapered to prevent galling in the reinforced Laird type crossheads. Grease cups are forged solid with the rod and off center to give a stronger construction. Pistons are of the Universal three-bull-ring type. Walschaert valve gears are supplied with an additional lever interposed between the radius rod and combination lever and pivoted at the rear end of the back valve cylinder head. This arrangement, covered by a patent application, magnifies the motion produced by the link but does not affect the motion produced by the combination lever and affords a longer valve travel than usual with Walschaert gear without exceeding the normal limits of angularity. The maximum travel obtained is nine inches, and in order to take full advantage of this travel and permit finer adjustments of cutoff, the Ragonnet power reverse gear is operated from the cab by a reverse lever and quadrant cut with more than the usual number of teeth.
The boiler of the new locomotive is designed for a minimum safety factor of four with a boiler pressure of 225 lb. It is of the wagon-top type, with conical barrel, the rear course of which is 99-15/16 in., and the first course 88 in. in outside diameter. The firebox has a grate area of 108 sq. ft. and is equipped with two 3-in. arch tubes, and two Nicholson thermic siphons. The combustion chamber is equipped with one thermic siphon. There are 221 superheater flues, 3-in. in diameter by 21 ft. long; and 59 tubes, 2-in. in diameter and of the same length. All of the superheater flues are electric welded to the back flue sheet and beaded in the front.
The wrapper sheet for this boiler is made in three pieces. The firebox and combustion chamber sides and crown sheet are also made in one piece and welded. The cast steel mud ring, double-riveted throughout, is arranged with a pad 1 in. thick to the underside of each corner and welded, inside and out, 12 in. each way from the corner. All firebox seams also are welded 50 in. up from the bottom of the sheets. Flannery flexible staybolts with universal sleeves are used in the breaking zones and completely around the combustion chamber, these bolts being hollow and arranged for electric testing.
In addition to the main steam dome, pressed from a single piece of openhearth steel, an auxiliary dome is located ahead of the main dome and far enough to the left of the boiler centerline so that the 9-in. inside dry pipe will not prevent entrance to the boiler for inspection or other purposes. The smokebox is of the extended type, 89-in. in outside diameter, with a pressed-steel front-end door and door ring hinged to the smokebox by an Okadee front-end hinge.
“Railway Mechanical Engineer” Article: In the Backshop and Enginehouse
Santa Fe Rebuilds Ten Locomotives
The Atchison, Topeka & Santa Fe has converted ten heavy 4-8-4 type steam locomotives, known as the 3751 class, at its Albuquerque, N.M., locomotive shops. These locomotives were purchased from Baldwin in 1928. They were originally stoker-fired, but a few years ago were changed to oil and this fuel continues in use. They will run through between La Junta, Colo., and Los Angeles, Cal., 1,235 miles. The conversion was completed in July.
The conversion work includes the following: Timken roller bearings applied to all wheels; new and longer smokebox applied; dome closed by inside cap, riveted in place; feedwater heater raised to smokebox location; reciprocating feedwater pump located under left side of cab; pressure raised from 220 to 230 lb.; two extra backhead braces and two extra flue sheet braces applied; size of radial stays around syphons increased; reinforcing pads riveted to barrel and smokebox; all rods new including tandem main rods, and new valve motion.
Boiler and Frames
The frames are the Commonwealth locomotive bed type. The pedestal jaws are straight to accommodate the Timken bearing housings that require no wedge, but use bronze-faced shoes between the frame and housing. In accordance with modern practice, the power reverse gear and air reservoirs are supported from the frame. The brackets for the latter are bolted to the frame and the bracket for the power reverse is included in the link bearer casting. The two belly braces are the floating type and the T-irons bear against heavy reinforcing pads riveted to the shell. The upright sheets of these braces are riveted to the T-irons and bolted to the integral cross members of the frame bed. There are three swing braces connecting the boiler and frame on each side. Two of these are on the smokebox and the other is on the shell.
In stripping, the boiler is cut loose from the cylinder saddle by burning off the heads of the bolts in the smokebox and burning out the part of these saddle bolts that extends through the smokebox. The heavy boiler work is done in the boiler shop. The original cast-steel cylinders are retained in the new design. The increase in pressure from 220 to 230 lb., necessitates two additional backhead braces and two additional back flue-sheet braces, and at this time the size of the radial stays around the siphons was increased to 1 3/16 in. body size. The original front-end throttle arrangement is unchanged and after the dome is permanently closed, entrance to the boiler is effected through an auxiliary dome. The original dome cap was slightly modified in shape (for clearance) and was placed inside the dome. The old stud holes in the dome are reamed and the cap riveted and caulked without the use of a gasket. This work was done while the flue sheet was out.
The increase in the length of the driving-wheel base to accommodate the 80-in. drivers makes a longer boiler necessary and a new smokebox 11 ft. long was rolled and applied in the local shop. New main steam pipes necessary between the superheater header and cylinders are several feet ahead of their former position in reference to the front flue sheet. There is little change in the draft appliances. An open-type spark arrester originally developed for coal burners by the Santa Fe test department is used with slight changes on oil burners, including the locomotives of the 3751 class.
Driving and Running Gear
Two outstanding additions in this connection are the change to tandem main rods, and the use of the Franklin Railway Supply Company’s patented lateral-motion device on the front drivers, made necessary on account of the long driving-wheel base. The front drivers have 3/8 in. total free lateral, and an additional movement of 11/16 in. in either direction, against spring action, is provided by the device. The necessary slack for this movement is provided between the roller-bearing housing (boxes) and the shoes. The lateral device centers the wheels by two rollers that extend through slots in the respective spring saddles. Each roller is mounted in a block which forms the inside saddle seat and the roller bears against part of the frame. The thrust of the wheels in rounding a curve is transmitted to one of these rollers which slightly tips the spring saddle against the resistance of the driver spring. The front end bushings have a spherical bearing in the rod to assure alignment. This device is also used on the front drivers of locomotive 5000, and many features of Santa Fe design that proved so successful on this locomotive are incorporated in the new design for the present conversion.
It is interesting to note that a new method has been developed for laying out the shoes which is different from the ordinary procedure in connection with shoes and wedges. This consists of squaring the frame in the usual way and locating accurately machined bars across the pedestal openings in the positions the axles will occupy. These bars are secured by small bolts to the spreaders that span the frame-jaw openings. The bars are adjusted square and in tram and the shoe thickness figured by measuring from the bars to the pedestal faces with micrometers. No prick punch marks are made on the shoes (which are not in place), but the milling-machine operator is supplied with dimensions in thousandths for each end of each shoe. The locomotive beds are accurately machined by the manufacturer and before the laying-out operation the distance between jaws is checked by offset measuring rods. The slight irregularities are corrected by filing and grinding and the jaws are spot faced. The shoes show little difference in size when finished.
Roller Bearings
Application of roller bearings in the shop is new for the Santa Fe and is an important addition and betterment. New tenders were applied to the 3751 locomotives at the time of change to oil and these had roller bearings as supplied by the builders. The present construction includes roller bearings for engine trucks, trailers, and drivers. Doing this work in the railroad shop requires the introduction of new standards of accuracy. Plus or minus .0015 in. is a common notation on the axle blueprints, and such close tolerances on the dimension of the cone-backing shoulders on axles require the use of special gages. These are the template type, made by Browne and Sharpe. One of these gages has its length stenciled 37.953125 in. A full set of inside and outside micrometers up to 14 inches is used at the axle lathe. The axles are of Timken design with liberal-radius fillets, and the wheel fit is smooth turned and polished for an inch or more inside the hub where experience and the Timken tests show that fatigue cracks develop. The fits for the bearing cones on the journal portion of the axle are ground on a Landis grinder.
Several new wheel-press jibs and fixtures are necessary to mount these bearings. For mounting outside journal truck bearings, a pilot sleeve is provided which fits over the axle stub. (About 1-in. at the end of the axle is reduced in diameter and takes a press fit collar). This pilot keeps the cone square as the fit enters. Heavy press fits on roller-bearing parts are not necessary or desirable. The thrust developed in rounding curves is transmitted to a shoulder on the axle, and unlike a wheel, the bearing parts do not depend on the fit alone to hold them in position. In mounting these parts little attention is paid to tonnage except that a maximum of 25 tons is mentioned. The fit allowance is carefully checked with micrometers and the proper amount of interference with .001 in. plus or minus is maintained. Castor oil and white lead are used as a lubricant on roller-bearing fits.
The exact procedure for mounting a Timken trailer bearing on outside bearings is as follows: For shipment the parts are covered with a light coat of oil. Before mounting, this protective coating is removed by washing the parts in distillate. The mounted wheels are placed in the wheel press as if the axle were to be pressed out. The enclosure (inner portion of housing) is placed over the axle against the hub with the bolts in place. This enclosure has four grooves on the inside which act as an oil seal and these are filled with valve oil to assure initial lubrication before the enclosure is applied. The oil flinger that supplements the seal is pressed in place. A freely fitting sleeve is used to press on these bearing parts. This sleeve has a spherical cap on the end toward the press ram to equalize pressure and prevent cocked the fitted parts. The first roller-bearing assembly, which includes the cone, rollers, and the flinger, is then pressed on, using the pilot fixture mentioned in a previous paragraph to start it straight. The cone spacing ring is applied next, and then the second roller bearing, after the cups are placed in position. The collar is then pressed on the end of the axle. The cup-spacing ring is in halves which may be fastened together by wire until the housing is slipped in place.
It is interesting to note that the rollers are within .0001 in. of the same size, and this size is etched on the large end of each roller. To check the lateral of the roller bearing, a dial indicator is used. The axle (inside journals) is turned on end preferably before the wheels are mounted and the bearing housing raised to the limit of its free motion. The load is released and the housing jarred down with a soft sledge. The dial indicator is clamped by a hand around the axle and indicates the lateral movement of the housing in thousandths.
Wheel Shop Practice
Press fits on the Santa Fe are lubricated with mineral paint (box car red) mixed with boiled linseed oil. A gallon of oil is used to thin 18 lb. of brown semi paste, which makes it about as thick as a priming coat of paint. This is prepared fresh each week, and is applied just before the parts are pressed together.
Counterbalancing
The method of counterbalancing at Albuquerque is essentially the same as followed in other large shops and locomotive works. The Boxpok main wheels have riveted plates covering the outside of the counterbalance space. These wheels are filled with lead before being mounted, while flat on the floor, and the lead is pounded with a long stroke riveting hammer to tighten it after it cools. All the wheels except the mains have solid steel counterweights, and three 3-in holes are drilled in the back of these for slight adjustment of the balance. The main wheels have cored holes in the back of the balance for the same purpose.
The main wheels and intermediate wheels are cross-balanced, 8 deg. and 59 min. on the main and 5 deg. and 59 min. on the number three. The counterbalances are off center this amount toward the opposite pin. When on the balancing strips, with the counterbalances perfectly adjusted, and the correct weight hung on the opposing pin, the main pin will be 27/16 in. out of plumb and the number three pin will be 1 11/16 out of plumb. After a while with a few trials it was possible to machine the wheels so accurately that changes of less than 50 lbs. (at pin radius) were required.